سیمان، طی شش مرحله اصلی شامل استخراج مواد خام از معادن، آسیاب کردن (به همراه توزین و مخلوط کردن)، اعمال حرارت اولیه، حرارت دادن در کوره، خنک سازی (به همراه آسیاب نهایی) و بسته بندی (به همراه انتقال به انبار) ساخته میشود. در ادامه، تمام مراحل اصلی ساخت سیمان را توضیح میدهیم.
مرحله اول: استخراج مواد خام سیمان از معادن
مواد خام مورد نیاز برای تولید سیمان، شامل سنگ آهک، ماسه یا رس (سیلیسیم، آلومینیوم، آهن)، شیل، خاکستر بادی، بوکسیت و غیره است. این مواد، سنگهای معدنی هستند که پس از استخراج، توسط سنگ شکن به قطعاتی با ابعاد حدود 15 سانتیمتر تبدیل میشوند. در مرحله بعدی، این قطعات برای رسیدن به ابعاد حدود 7 سانتیمتر در فرآیند سنگ شکنی ثانویه قرار میگیرند. به این ترتیب، قطعات سنگی خرد شده برای مرحله بعدی آماده میشوند.
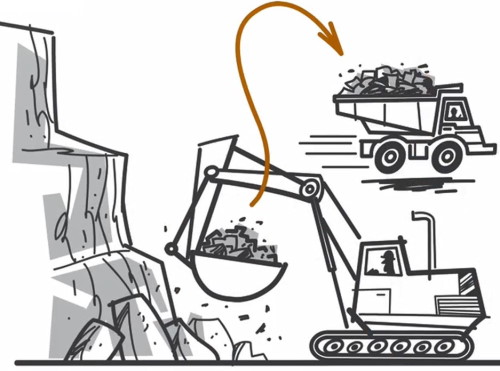
مرحله دوم: آسیاب، توزین و مخلوط کردن
با آسیاب کردن مواد اولیه خرد شده در مرحله قبل و اضافه کردن مواد شیمیایی و افزودنیهای مورد نظر، یک مخلوط همگن کوچکتر تشکیل میشود. توزین ذرات در این مرحله با توجه به خواص مورد نیاز صورت میگیرد. معمولا 80 درصد این مخلوط از سنگ آهک و 20 درصد باقیمانده آن از رس تشکیل میشود. فرآیند خشک کردن مخلوط مواد خام نیز تا رسیدن رطوبت آن به زیر 1 درصد در کارخانه صورت میگیرد. سپس، غلتکهای بزرگ و میزهای گردان، مخلوط مواد خام را خرد کرده و بهم میزنند. در نهایت، پودر ریزی به دست میآید که برای انتقال به کوره آماده است.
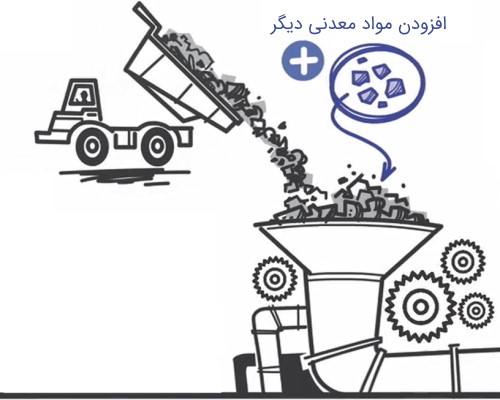
مرحله سوم: اعمال حرارت اولیه به مواد خام
برای اعمال حرارت اولیه، مواد خام به محلی با چندین سیکلون انتقال داده میشوند. این سیکلونها با استفاده از گازهای داغ تولید شده از طرف کوره، حرارت اولیه را به مواد خام انتقال میدهند. هدف از این فرایند، کاهش مصرف انرژی و آلودگی محیط زیستی است. در این مرحله، مواد خام با عبور از سیکلونها به مواد اکسیدی تبدیل شده و آماده پخت در کوره میشوند.

مرحله چهارم: پخت مواد خام در کوره (تشکیل کلینکر)
در فرآیند تولید سیمان، پخت مواد خام در کوره، اصلیترین مرحله به شمار میرود. در این مرحله، طی انجام چندین واکنش شیمیایی بین ترکیبات کلسیم و سیلیسیم دی اکسید، مادهای به نام کلینکر تشکیل میشود.
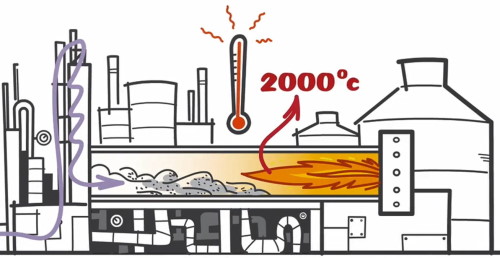
با وجود پیچیده بودن این فرآیند، مراحل تولید کلینکر را میتوان به صورت زیر خلاصه کرد:
- تبخیر آب آزاد
- تبخیر آب موجود در ترکیبات رسی
- تبدیل کربنات کلسیم (CaCO3) به اکسید کلسیم (CaO) طی فرآیند کلسیناسیون
- تشکیل دی کلسیم سیلیکات بر اثر واکنش CaO با سیلیسیوم
- تشکیل فاز مایع بر اثر واکنش CaO با آلومینیوم و ترکیبات دارای آهن
- تشکیل دانههای کلینکر
- تبخیر مواد فرار (نظیر سدیم، پتاسیم، کلریدها و سولفاتها)
- تشکیل تری کلسیم سیلیکات بر اثر واکنش CaO اضافی با دی کلسیم سیلیکات
فرآیندهای بالا را میتوان بر اساس تغییر دمای درون کوره به چهار بخش تقسیم کرد:
- دمای 100 درجه سانتیگراد: بخار آب آزاد
- دمای 100 تا 430 درجه سانتیگراد: کاهش آب و تشکیل اکسیدهای سیلیسیوم، آلومینیوم و آهن
- دمای 900 تا 982 درجه سانتیگراد: آزاد شدن CO2 و تشکیل CaO بر اثر کلسیناسیون
- دمای 1510 درجه سانتیگراد: تشکیل کلینکر
واکنشهای شیمیایی بین مواد موجود در کوره بعد از بخار آب شروع میشوند. این واکنشها به ترتیب عبارت هستند از:
- تجزیه رس
- تجزیه دولومیت
- تجزیه کلسیت در دمای پایین
- واکنش آلومینا و اکسیژن
- واکنش کلسیت باقی مانده
- «سینترینگ» (Sintering) یا تف جوشی
کوره پخت سیمان، سه درجه نسبت به سطح افق زاویه دارد. این زاویه امکان عبور مواد خام از درون کوره را در مدت 20 تا 30 دقیقه فراهم میکند. با رسیدن مواد خام به پایینترین بخش، دانههای کلینکر با شکلی مشابه قلوه سنگ از درون کوره خارج میشوند.
مرحله پنجم: خنک سازی و آسیاب نهایی
با خروج کلینکر از درون کوره و تماس با هوای آزاد، دمای آن به سرعت از 2000 درجه سانتیگراد به 100 تا 200 درجه سانتیگراد میرسد. در این مرحله با آسیاب کردن مجدد کلینکر، چندین ماده مختلف به ترکیب اضافه میشود تا محصول نهایی (سیمان) به دست آید. سنگ گچ به منظور تعدیل زمان گیرش و مقاوم سازی به کلینکر اضافه و به همراه آن آسیاب میشود. به علاوه، این ماده از چسبیدن ترکیب به بدنه و گلولههای آسیاب جلوگیری میکند. مواد دیگری نظیر تری اتانول آمین نیز به منظور ریز شدن بهتر مواد و جلوگیری از گوله شدن آنها مورد استفاده قرار میگیرند.
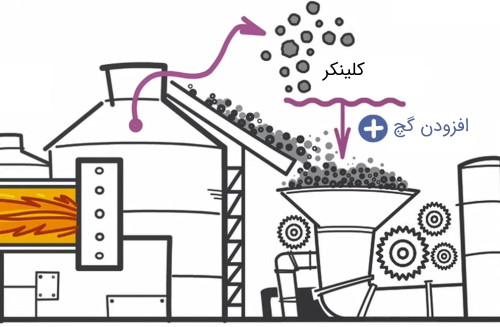
به منظور صرفه جویی در مصرف انرژی، حرارت ایجاد شده توسط کلینکر به کوره بازمیگردد. آخرین مرحله از تولید سیمان، فرآیند آسیاب کردن نهایی است. در کارخانه سیمان، طبلکهای گردانی به همراه گلولههای فولادی وجود دارند. پس از فرآیند خنک شدن، کلینکر به درون این طبلکها منتقل میشود. با اتمام آسیاب نهایی، پودر ریزی به دست میآید که هر کیلوگرم از آن شامل 75 میلیون ذره است. این پودر، سیمان نام دارد.
مرحله ششم: بسته بندی و انتقال به انبار
در این مرحله، سیمان در بستههای 20 تا 40 کیلوگرمی بستهبندی شده و از محل آسیاب به سیلوهای مخصوص انتقال داده میشود. البته اکثر سیمان تولید شده در مقادیر بالا توسط کامیون، قطار یا کشتی به محلهای مورد نیاز انتقال مییابند و فقط مقدار کمی از آن به صورت بستهبندی شده به مشتریان تحویل داده میشود.
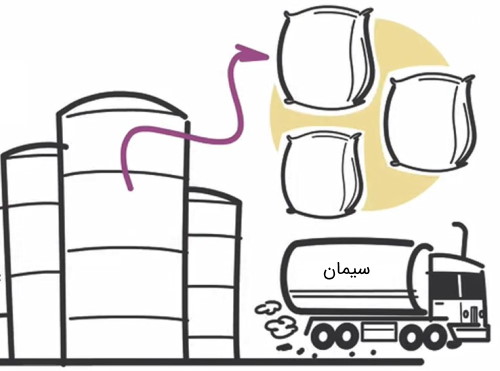